Automation from a batch size of one
Since Horlemann Gesellschaft für Elektroanlagen mbH has been planning its switch cabinets using EPLAN Pro Panel, the company has benefited from shorter throughput times in the electrical workshop.
Since Horlemann Gesellschaft für Elektroanlagen mbH has been planning its switch cabinets using EPLAN Pro Panel, the company has benefited from shorter throughput times in the electrical workshop. The 3D planning makes it possible to prepare the processes more exactly, and also provides more standardisation. This is appreciated by customers who work in areas such as energy supply, water/waste water engineering and the bulk materials industry. Sieving, mixing, metering, conveying, weighing: Many companies make use of the expertise of Horlemann Gesellschaft für Elektroanlagen mbH in Uedem. Horlemann develops hardware and software for automating continuous processes that are used in areas such as the bulk materials industry, water and waste water engineering and in food production. Switch cabinet construction therefore plays a significant role. State-of-the-art ECAD tools - from the start
The company gives its automation engineering customers the advantage of: "Everything from a single source". Project Manager Thomas Willems explains: "We adapt our software to existing interfaces, plan the entire hardware infrastructure and plan and construct the switch cabinets in-house." From a customer point of view, this means consistent processes implemented by a single contact, who is therefore in a position to automate entire waste water systems, gravel plants or food production lines. Consistent switch cabinet manufacture, from engineering to production
This consistency is also reflected at planning level. Here, the company always uses the latest tools. Says Willems: "Since we were established in 1989, our electronic engineers have been working with EPLAN and always use the latest releases." Shortly after the launch of EPLAN Electric P8, Horlemann migrated to the new EPLAN Platform. And when solution provider EPLAN introduced the latest system of the platform, "Pro Panel Professional" in mid-2011, the company obtained information without delay and decided on quick introduction.
This means that the system is now introducing 3D technology into projects and works on the same data basis as EPLAN Electric P8. The project data is therefore "passed through" from the schematics to the 3D cabinet layout and then to production. EPLAN Pro Panel makes it possible to carry out three-dimensional switch cabinet planning with virtual wiring, including all of the advantages such as automatic routing, exact component placement and collision monitoring. Since all the dimensions are known, the switch cabinet is planned with millimetre accuracy, and all cabling is carried out accurately and with length optimisation. The system also creates the prerequisite for absolute consistency throughout the entire planning process to the installation of the switch cabinet: The data from Pro Panel can be passed directly to the machines for NC sheet metal machining and cable assembly. 100% compliance of circuit diagrams and switch cabinets
In order to make optimum use of this consistency in product development, when Horlemann purchased EPLAN Pro Panel in September 2011 it also invested in two Steinhauer cable assembly machines. The company has already taken some positive steps in direct linking of production systems: the sheet metal processing centre that was purchased one and a half years ago has been directly actuated via the EPLAN Platform since commissioning took place. Horlemann has succeeded in implementing new work procedures by combining EPLAN Pro Panel with automatic cable assembly. Electrical designer Volker Hellmann: "When switch cabinet planning was still being carried out in 2D, the cost of manufacturing was significantly higher. The specifications were inaccurate and the solutions were inconsistent. This sometimes led to queries if, for example, our customers were collaborating with engineering offices that closely checked the correspondence of documentation and electrical circuit diagrams. The wiring is also carried out exactly according to plan. We therefore achieve a high degree of standardisation and a higher quality level, which is appreciated by our customers.” New work processes in electrical planning and workshops
More detailed planning results in the workshop being provided with better information. The placement of the components is also specified, as are the cable length and the cable routing. Willems explains: "This simplifies working procedures in manufacturing considerably, since the manufacturing drawings leave nothing to be desired." The interaction between EPLAN Pro Panel and automatic cable assembly is extremely effective. The worker takes the cable out of the Steinhauer machine, acknowledges the procedure, looks on the screen of the machine and connects the cable in the intended location within seconds. In the meantime, the machine has already made the next cable. In order to simplify the labelling, mobile Phoenix printers have been purchased which are actuated by the Phoenix "Clip Project" software (which also uses data from the EPLAN Platform). "This reduces the cost of labelling considerably,” says Hellmann. “We generate the single-wire labels on site and attach them immediately, and also other types of labelling for terminals, wires, lamps and doors, for example. In the past we often had these signs engraved externally, with the result that they were wrong or delivered too late and had to be sent again." Increase in master data resources
The lead time before the initial use of EPLAN Pro Panel was extremely short. Hellmann built up a basic structure of standard components and modules. "The majority of the data is added during construction by entering the component dimensions, for example, or downloading appropriate files from the manufacturer web sites. In this way we are systematically expanding our database of 3D data records. When doing this the electrical designers ensure that granulation does not go beyond component level. We have created our own symbol macros, but no assembly macros. There are not enough repeated assemblies in our projects." Automation from a batch size of one, and 20% faster
You have to ask the question: Is automation worth it if you always manufacture in batch sizes of one? At Horlemann there is an unequivocal answer to this question. "It is particularly worth it in this case,” says Hellmann. “With series production you can always streamline or delegate to a job manufacturer. With individual projects the streamlining potential is in process automation and the consistency of the processes. This can even be proven with statistics.” Willems adds: "When we had to manufacture two switch cabinets that were the same, we ran a test: One switch cabinet was manufactured using the old method, and the other with the new method. The new process was 20% faster." Horlemann Gruppe: Bundled expertise in electrical engineering and energy supply
The Horlemann Gesellschaft für Elektroanlagen mbH is one of several subsidiaries of the Horlemann Group, which has around 550 employees and is managed by the third generation of the family that founded the company. The heavy equipment in the courtyard of the company such as lorries, trailers and containers are used by the other subsidiaries, which work in the electrical engineering and pipeline and systems engineering areas. Another business area is mobile power supplies – Horlemann sets up temporary power systems that supply power to entire football stadia or major events, for example. The group is also involved in the manufacture of transformers and medium voltage switchgear. This business area also utilises the EPLAN Platform for planning.
Since Horlemann Gesellschaft für Elektroanlagen mbH has been planning its switch cabinets using EPLAN Pro Panel, the company has benefited from shorter throughput times in the electrical workshop. The 3D planning makes it possible to prepare the processes more exactly, and also provides more standardisation. This is appreciated by customers who work in areas such as energy supply, water/waste water engineering and the bulk materials industry. Sieving, mixing, metering, conveying, weighing: Many companies make use of the expertise of Horlemann Gesellschaft für Elektroanlagen mbH in Uedem. Horlemann develops hardware and software for automating continuous processes that are used in areas such as the bulk materials industry, water and waste water engineering and in food production. Switch cabinet construction therefore plays a significant role. State-of-the-art ECAD tools - from the start
The company gives its automation engineering customers the advantage of: "Everything from a single source". Project Manager Thomas Willems explains: "We adapt our software to existing interfaces, plan the entire hardware infrastructure and plan and construct the switch cabinets in-house." From a customer point of view, this means consistent processes implemented by a single contact, who is therefore in a position to automate entire waste water systems, gravel plants or food production lines. Consistent switch cabinet manufacture, from engineering to production
This consistency is also reflected at planning level. Here, the company always uses the latest tools. Says Willems: "Since we were established in 1989, our electronic engineers have been working with EPLAN and always use the latest releases." Shortly after the launch of EPLAN Electric P8, Horlemann migrated to the new EPLAN Platform. And when solution provider EPLAN introduced the latest system of the platform, "Pro Panel Professional" in mid-2011, the company obtained information without delay and decided on quick introduction.
This means that the system is now introducing 3D technology into projects and works on the same data basis as EPLAN Electric P8. The project data is therefore "passed through" from the schematics to the 3D cabinet layout and then to production. EPLAN Pro Panel makes it possible to carry out three-dimensional switch cabinet planning with virtual wiring, including all of the advantages such as automatic routing, exact component placement and collision monitoring. Since all the dimensions are known, the switch cabinet is planned with millimetre accuracy, and all cabling is carried out accurately and with length optimisation. The system also creates the prerequisite for absolute consistency throughout the entire planning process to the installation of the switch cabinet: The data from Pro Panel can be passed directly to the machines for NC sheet metal machining and cable assembly. 100% compliance of circuit diagrams and switch cabinets
In order to make optimum use of this consistency in product development, when Horlemann purchased EPLAN Pro Panel in September 2011 it also invested in two Steinhauer cable assembly machines. The company has already taken some positive steps in direct linking of production systems: the sheet metal processing centre that was purchased one and a half years ago has been directly actuated via the EPLAN Platform since commissioning took place. Horlemann has succeeded in implementing new work procedures by combining EPLAN Pro Panel with automatic cable assembly. Electrical designer Volker Hellmann: "When switch cabinet planning was still being carried out in 2D, the cost of manufacturing was significantly higher. The specifications were inaccurate and the solutions were inconsistent. This sometimes led to queries if, for example, our customers were collaborating with engineering offices that closely checked the correspondence of documentation and electrical circuit diagrams. The wiring is also carried out exactly according to plan. We therefore achieve a high degree of standardisation and a higher quality level, which is appreciated by our customers.” New work processes in electrical planning and workshops
More detailed planning results in the workshop being provided with better information. The placement of the components is also specified, as are the cable length and the cable routing. Willems explains: "This simplifies working procedures in manufacturing considerably, since the manufacturing drawings leave nothing to be desired." The interaction between EPLAN Pro Panel and automatic cable assembly is extremely effective. The worker takes the cable out of the Steinhauer machine, acknowledges the procedure, looks on the screen of the machine and connects the cable in the intended location within seconds. In the meantime, the machine has already made the next cable. In order to simplify the labelling, mobile Phoenix printers have been purchased which are actuated by the Phoenix "Clip Project" software (which also uses data from the EPLAN Platform). "This reduces the cost of labelling considerably,” says Hellmann. “We generate the single-wire labels on site and attach them immediately, and also other types of labelling for terminals, wires, lamps and doors, for example. In the past we often had these signs engraved externally, with the result that they were wrong or delivered too late and had to be sent again." Increase in master data resources
The lead time before the initial use of EPLAN Pro Panel was extremely short. Hellmann built up a basic structure of standard components and modules. "The majority of the data is added during construction by entering the component dimensions, for example, or downloading appropriate files from the manufacturer web sites. In this way we are systematically expanding our database of 3D data records. When doing this the electrical designers ensure that granulation does not go beyond component level. We have created our own symbol macros, but no assembly macros. There are not enough repeated assemblies in our projects." Automation from a batch size of one, and 20% faster
You have to ask the question: Is automation worth it if you always manufacture in batch sizes of one? At Horlemann there is an unequivocal answer to this question. "It is particularly worth it in this case,” says Hellmann. “With series production you can always streamline or delegate to a job manufacturer. With individual projects the streamlining potential is in process automation and the consistency of the processes. This can even be proven with statistics.” Willems adds: "When we had to manufacture two switch cabinets that were the same, we ran a test: One switch cabinet was manufactured using the old method, and the other with the new method. The new process was 20% faster." Horlemann Gruppe: Bundled expertise in electrical engineering and energy supply
The Horlemann Gesellschaft für Elektroanlagen mbH is one of several subsidiaries of the Horlemann Group, which has around 550 employees and is managed by the third generation of the family that founded the company. The heavy equipment in the courtyard of the company such as lorries, trailers and containers are used by the other subsidiaries, which work in the electrical engineering and pipeline and systems engineering areas. Another business area is mobile power supplies – Horlemann sets up temporary power systems that supply power to entire football stadia or major events, for example. The group is also involved in the manufacture of transformers and medium voltage switchgear. This business area also utilises the EPLAN Platform for planning.
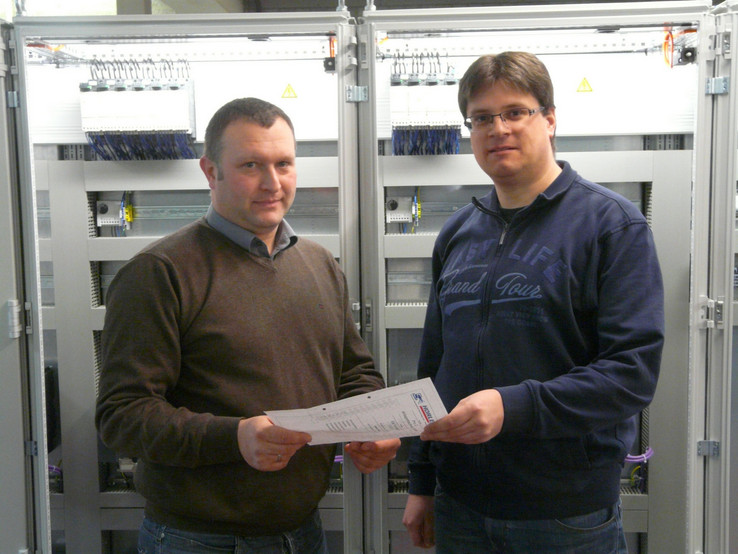
Thomas Willems, project leader at Horlemann Gesellschaft für Elektroanlagen mbH (left) and designer Volker Hellmann (right) have built up a consistent process chain from planning via all stages of engineering and manufacturing through to cable assembly.
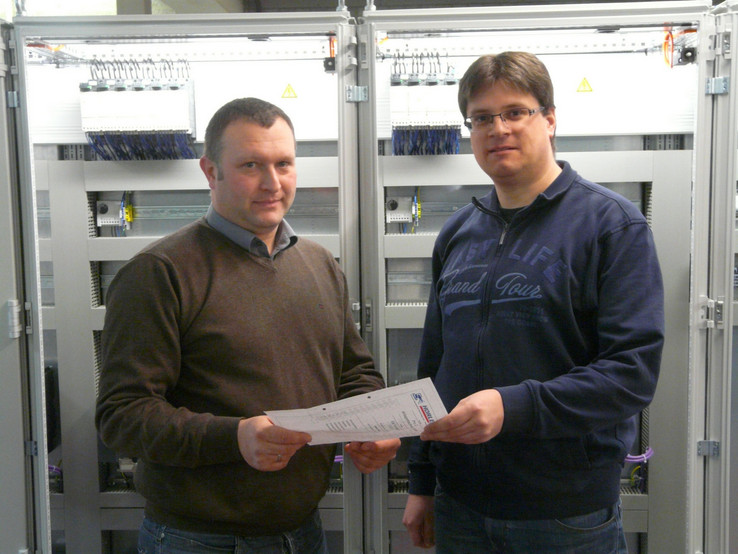
Thomas Willems, project leader at Horlemann Gesellschaft für Elektroanlagen mbH (left) and designer Volker Hellmann (right) have built up a consistent process chain from planning via all stages of engineering and manufacturing through to cable assembly.